Hydraulic stamping technology is transforming modern kitchen sink manufacturing. It delivers exceptional forming precision and production efficiency, helping manufacturers overcome traditional limitations. By integrating advanced equipment and cutting-edge processes, hydraulic technology enables stainless steel sink production to achieve significant improvements in both design and performance.
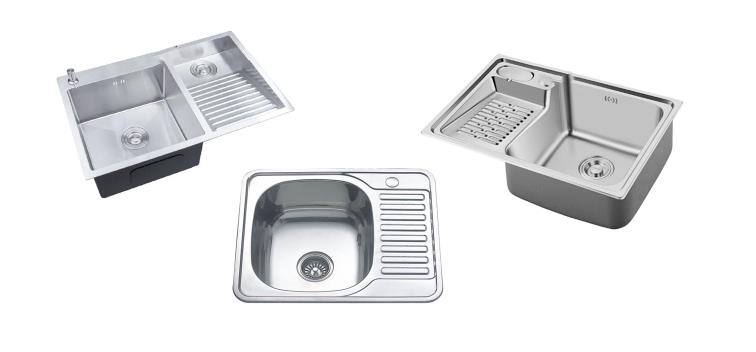
Revolutionary Hydraulic Forming Process
Traditional sink production often depends on manual bending and welding, leading to low efficiency and issues like weld deformation. Hydraulic technology solves these challenges by offering a more efficient, precise, and flexible solution. The integrated stretching process forms 0.8-1.0mm stainless steel sheets under 200-1500-ton hydraulic pressure, eliminating the need for welding. For complex structures such as deep basins and small-radius corners (R≤25mm), the equipment uses intelligent speed control. The system accelerates during the idle stroke and switches to precision mode as soon as it contacts the material, ensuring complete control over material flow. This results in a 220mm basin depth and a 30% improvement in space utilization. Advanced compound stretching coordinates multi-stage processes, combining segmented forming with precision welding. This method breaks the 1.0mm thickness barrier while keeping wall thickness uniform (error ≤0.1mm) and reducing flange height to 5-6mm for better countertop sealing.
Precision-Engineered Hydraulic Presses
Our hydraulic equipment series offers pressure ranges from 400 to 1500 tons, covering a variety of production needs. The 400-ton four-column press integrates PLC control with a touchscreen interface, enabling stepless adjustment of drawing and blank holder forces. For heavier-duty applications, the 1500-ton frame press features anti-deflection reinforcement and optional laser calibration modules for specialized tasks. The system also includes a triple safety protection system—mechanical limit blocks, infrared light curtains, and hydraulic emergency locks—that ensures safe operation over 20,000 continuous cycles.
Beyond Kitchens: Cross-Industry Impact
As market demands for ultrathin walls and large-capacity sinks increase, hydraulic technology extends its benefits beyond kitchen manufacturing. Innovative compound stretching combines kiloton pre-stretching (thinning rate ≤8%) with precision sidewall forming to create reinforced 5° inclined structures. Manufacturers finish these structures with laser-sealed edges that meet food-grade standards. This process results in a 190mm single-basin depth, with a 30% capacity increase and panel flatness error under 0.1mm. Modular die systems enable quick texture changes, allowing manufacturers to switch between brushed, matte, or 3D patterns. This improves pattern uniformity by 60%. In industrial applications, the system processes 1,500×900mm sheets with just two operators and achieves a daily output of 40 units, cutting overall costs by 50%.
Engineer Your Zero-Defect Future Today
Hydraulic technology drives the shift to zero-defect manufacturing. By embracing precision, process innovation, and cost restructuring, manufacturers can reduce scrap rates to below 0.2% using real-time deformation simulation. Contact our engineering team today to customize hydraulic press solutions that will optimize your production efficiency and take your manufacturing capabilities to the next level.
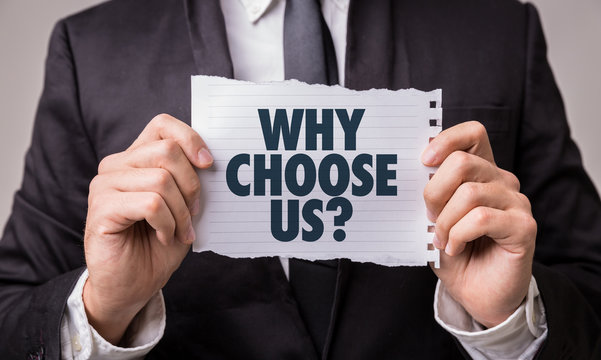